Kui mitmed tehased on võtnud eesmärgiks täisautomatiseeritud inimtööjõuvaba targa tehase, siis Porsche Stuttgardi sportautode valmimisliini külastades kinnitas nende esindaja Christian Weiss, et autosid jäävad alati kokku panema inimesed koostöös automaatsete süsteemidega.
See aga ei tähenda, et tehas ei oleks võtnud juba praegu kasutusele lahendusi, mis inimeste tööd kergemaks muudavad. Porsche Stuttgardi tehases toodetakse kolme sportauto mudelit. Ruumipuudusel on ülejäänud mudelite tootmine viidud Saksamaa Leipzigi tehasesse. Kuigi autosid on kõige mõistlikum toota ühel tasapinnal, siis legendaarsete sportautode tootmisliin jookseb Stuttgardis läbi kahe korruse.
Kokku on Stuttgardi Porsche tehasekompleksis viis hoonet, mille vahel on jagatud autode eri osade kokkupanek. Komponente kohapeal ei toodeta, neid ei tooda mitte laohoonesse, vaid kohapealsesse n-ö supermarketisse vastavalt sellele, missuguste autode tellimused täitmist ootavad.
Üle poolesaja tuhande auto
Ühes päevas valmib 250 autot, eelmisel aastal valmis tehases kokku ca 55 000 autot. Ühe auto valmimine alates värvimisest kuni mootori ja detailide paigaldamiseni võtab aega 4–5 päeva. Kõik autod, mis tehasest välja sõidavad, on valminud eritellimusel ning liini peal väga suure tõenäosusega kahte ühesugust autot järjest ei tehta.
Eritellimusel valmivat Porsche sportautot tuleb Porsche Eesti esindaja Lemmo Tigase sõnul oodata 3–6 kuud. Ehkki esinduses on alati olemas teatud autovalik, siis seda tüüpi auto ostja enamasti siiski ikkagi tellib auto ja kujundab selle vastavalt oma soovidele. Valida saab nii auto värvi, istmete nahatooni, kasutatud õmblusi kui ka loomulikult kogu sõiduks vajalikku elektroonikat.
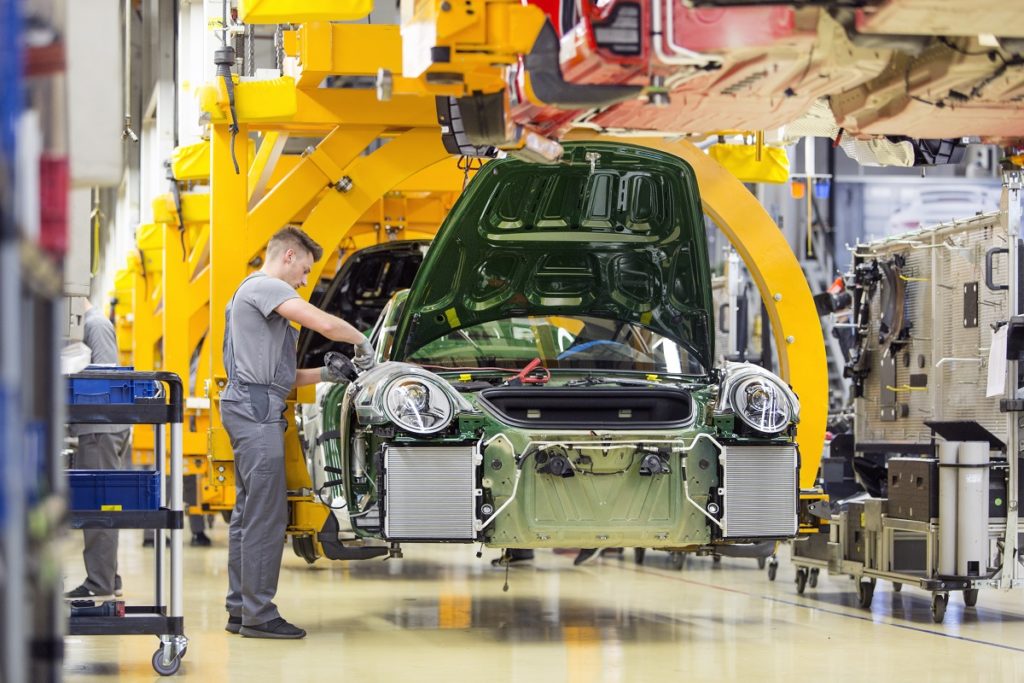
250
autot valmib tehases ühe päevaga.
Tööriistad koodi alusel
Tootmine on jagatud erinevate hoonete vahel. Eraldi hoone on mootorite kokkupanekuks. Mootoreid on selles tehases valmivate mudelite jaoks kolme tüüpi: V-, Boxer-tüüpi ja GT3 mootorid, mille jaoks on oma tootmisread. Iga rida liigub automaatselt robotite abil, kuid iga mootori valmimise eest vastutab üks inimene, erandjuhtudel kuni kolm.
Seda osa, mida robotid teha ei saa, teevad inimesed ise. Töö kergendamiseks on mootori kokkupanekul iga etapi tööriistad standardiseeritud. Veelgi enam – et ühtki viga ei tekiks, on enne tööriista kasutamist vaja skaneerida QR-kood ning asetada tööriist õige nurga alla. Enne tööriist tööle üldse ei lähegi. See tagab, et kõik ühendused on tehtud õige nurga alt ning toimivad laitmatult.
Enne veel, kui autod tootmisliinil kokku pannakse, värvitakse kereosad teises hoones ning transporditakse iga kümne minuti järel tootmisliinile. Liin liigub koos järjest valmiva autoga aeglaselt ja katkematult läbi kõigepealt teise ja seejärel esimese korruse, kus 25. tööpostil toimetavad autoga eraldi meeskonnad – kokku tuhatkond inimest, kes vastutavad autode kaabelduse, juhtpaneeli, istmete, akende paigalduse ning kereosa šassiiga ühendamise eest.
Stressivaba töökeskkond
Tootmishoones liini kõrval on sõiduteed, mida kasutavad komponentide transpordiks automatiseeritud veokid, mis transpordivad tööpostidele vajalikku. Veokid on programmeeritud sõitma oma kindlat trajektoori ning leiavad õige teeotsa maha joonistatud mustade pidevjoonte abil. Triipkoodi abil kontrollitakse kõigis etappides, mis automudeliga on tegu ja kas osad, mis kohale on sõitnud, vastavad sellele mudelile.
Töö tootmisliinil on paika seatud lausa minuti täpsusega. Igas meeskonnas töötab alati keegi kogenum uue töötaja kõrval: vea tekkimine selles täpses tantsuskeemis tähendaks kogu liini seiskamist ja töökatkestust mitmeks tunniks.
Töötajate liigutused on rahulikud ja täpsed, stressi ega kiirustamist ei paista. Ühes tunnis on töötajatele ette nähtud 5-minutiline paus, mille jooksul võib lihtsalt jalga puhata kui ka soovi korral rutiini vältimiseks meeskonda vahetada.
Ainus töökoda, kus sellist ranget ajapiirangut ei seata, on nahatöökoda. Sealsetele töötajatele antakse tellimus üks päev ette. Tegemist on kõige vähem automatiseeritud tööetapiga, kus seinal isegi kiri „Handwerk 4.0“.
Enne kui auto liini pealt maha sõidab, testivad töötajad, kas kõik töötab ning edasi suundub auto edasi 30 km pikkusele testsõidule. Seejärel ootab kaitsekilesse pakitud tuliuusi Porschesid juba veoautosõit müügipunktidesse.
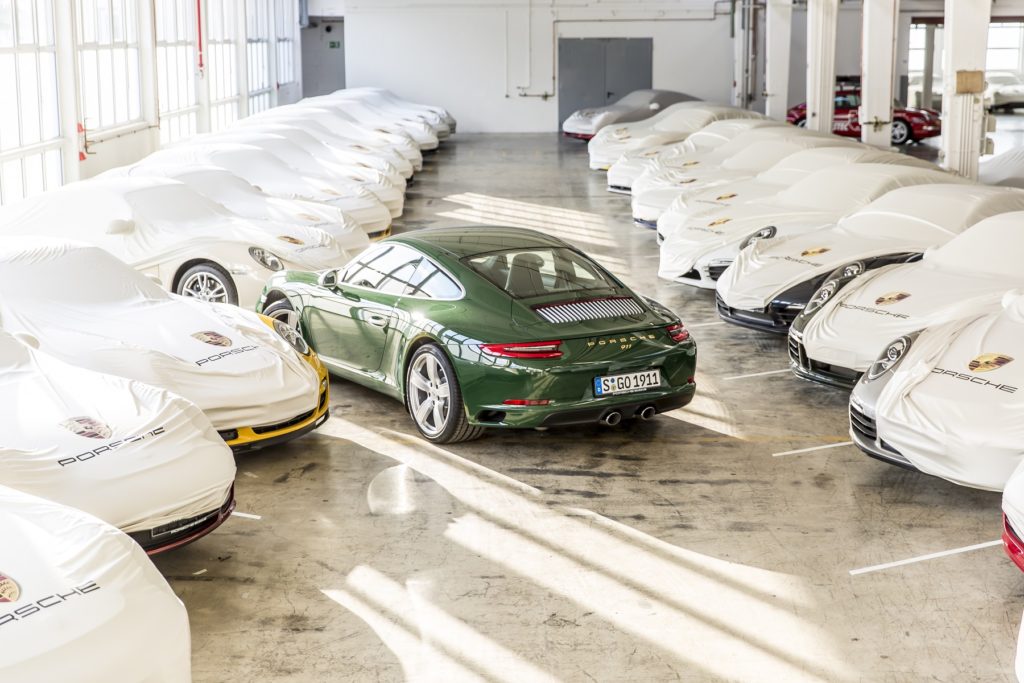
Nutikas kokkuhoiunipp Agfa-Gevaert Grupilt
Lõuna-Saksamaal, täpsemalt Peissenbergis asuv meditsiiniseadmete ja röntgenaparaatide tootja Agfa on tööle pannud lihtsa ning nutika süsteemi, kuidas vähendada laovarude koguseid, tutvustas tehase juht Herbert Klein.
Ühes päevas saadetakse tehasest välja kuni 40 seadet või masinat. Nende pakkimiseks kuluva pakkematerjali hoiustamisele kuluks terve laopind.
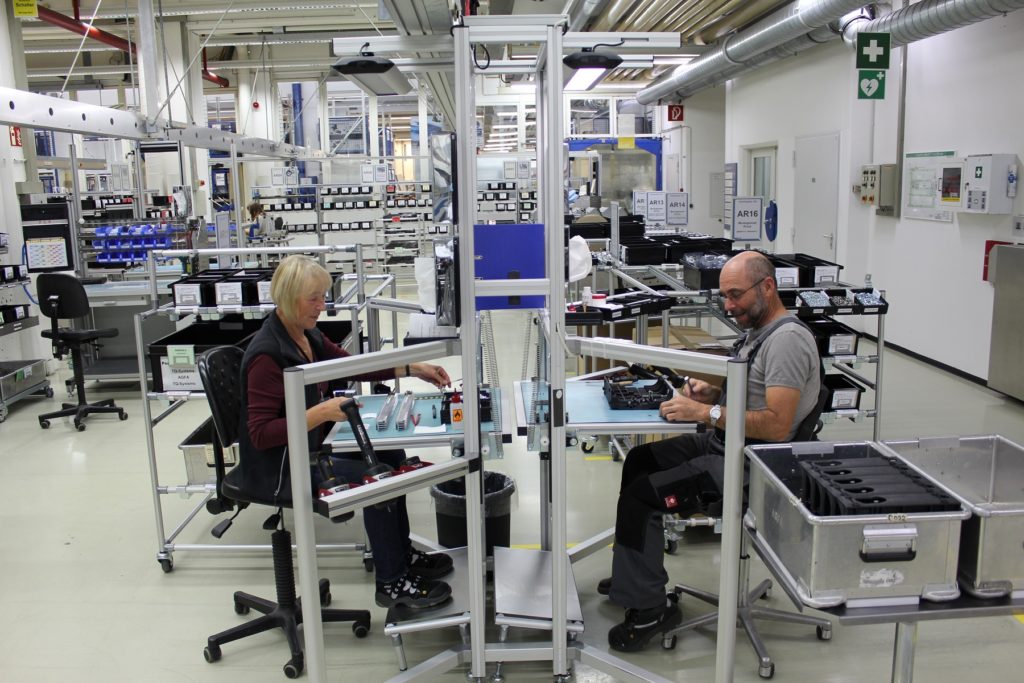
Selle asemel on ettevõte sõlminud lepingu teenusepakkujaga, kes jälgib veebikaamera abil reaalajas pakkematerjalide seisu ja hindab varude täiendamise vajadust. Igal hommikul toob teenusepakkuja hinnanguliselt vajamineva pakkematerjalide koguse ning täiendab seda päeva jooksul vajaduse korral.
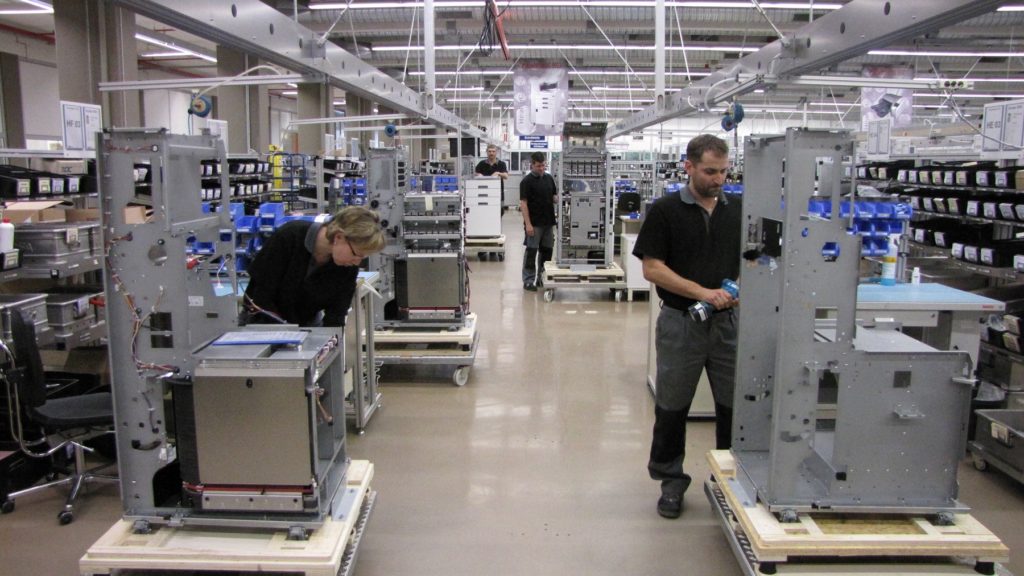
Agfa töötajad on jagatud kokku 18 meeskonda, kellest igaüks vastutab teatud tootmisetapi eest. Agfa tehase juht Herbert Klein võrdles tehasetööd jalgpalliga, kus kõigil on oma roll ja vastutus. Treener on väljaku kõrval aga abiks ja toeks ning tema töös otseselt ei osale. Kõigile on seatud nõue tagada oma töö kvaliteet, mistõttu puudub vajadus täiendava kontrolli järele. Ettevõtte jaoks tähendab see kokkuhoidu, kuna kvalifikatsiooni säilitamise jaoks on tarvis pidevalt lasta end erinevatel organisatsioonidel auditeerida.
Saksa-Balti Kaubanduskoda (AHK) korraldas ajakirjanikele pressireisi Lõuna-Saksamaal asuvale Baierimaale, et tutvustada Industrie 4.0 lahendusi. Projekti toetas Saksa välisministeerium.